Exploring the World of Machining Lathe Parts Factories
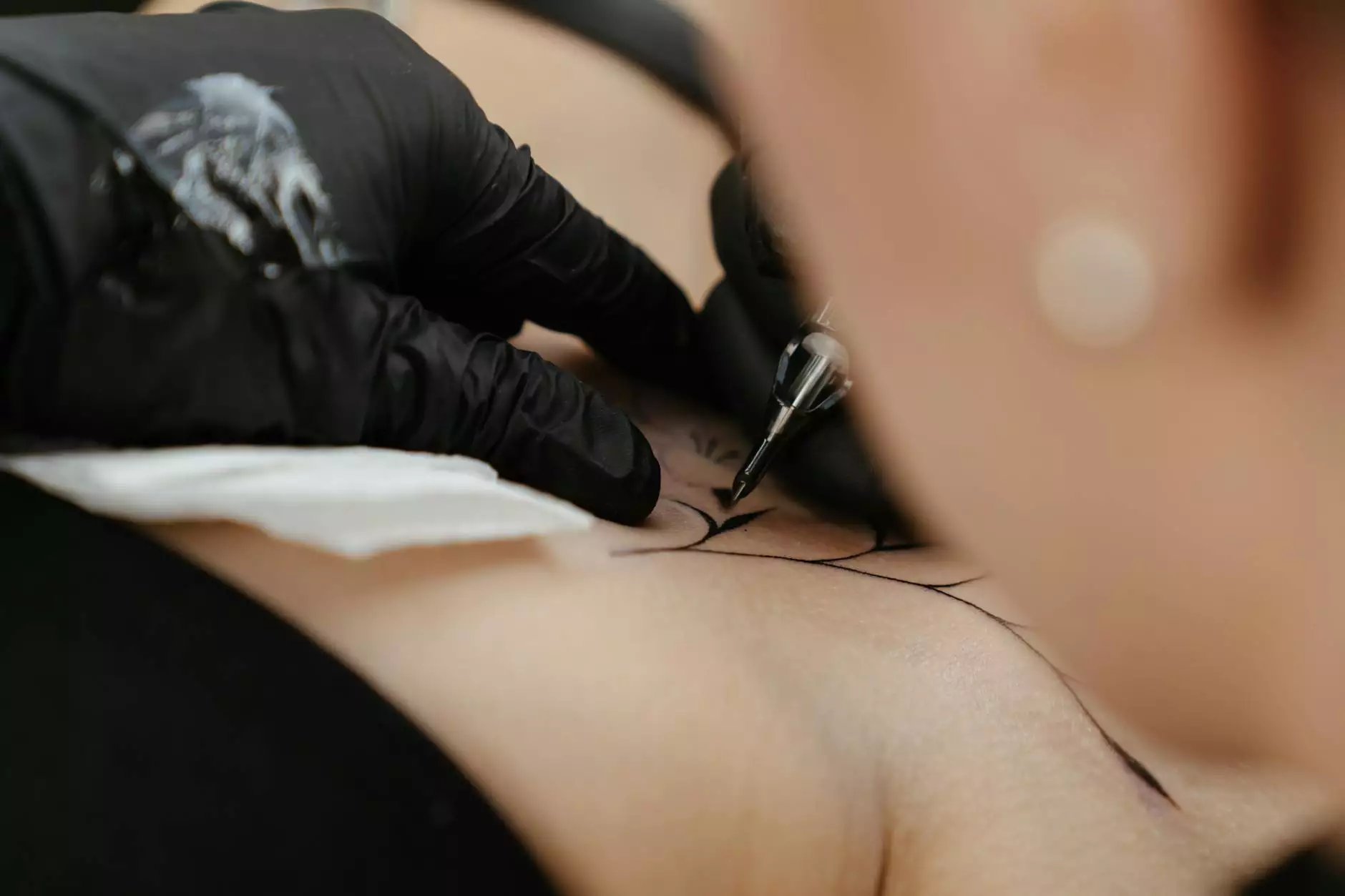
The landscape of machining lathe parts factories has evolved significantly over the years. With the advancement of technology and an increasing demand for precision engineering in various industries, the role these factories play is more crucial than ever. This article delves into the nuances of machining lathe parts, the technologies involved, the benefits they offer, and their future in the manufacturing sector.
Understanding Machining Lathe Parts
Machining lathe parts are essential components produced through a process known as turning. This technique involves the rotation of a workpiece while a cutting tool removes material, resulting in a precise shape. The accuracy offered by machining lathe operations is vital for creating parts used in various applications, from automotive to aerospace.
The Process of Machining Lathe Parts
The process of machining lathe parts can be broken down into several key steps:
- Preparation: Selecting the appropriate material based on strength, weight, and corrosion resistance.
- Setting Up: Mounting the workpiece onto the lathe and configuring the machine settings for optimal operation.
- Turning: Engaging the lathe to begin the turning process, which involves feeding the cutting tool along the material.
- Finishing: Applying finishing techniques to improve surface quality and dimensional accuracy.
- Quality Control: Conducting thorough inspections to ensure each part meets specified tolerances.
Types of Machined Lathe Parts
Machining lathe parts come in various forms, each serving unique purposes across different industries. Some common types include:
- Shafts: Used in rotating machinery, often requiring high precision.
- Housings: Enclosures for mechanical components, requiring complex shapes and tolerances.
- Bushings: Tolerances are critical, especially in applications where they serve as guides or bearings.
- Gears: Critical for transmitting motion and power in machinery.
- Custom Parts: Tailored components designed to meet the exact specifications of a client's project.
Benefits of Machining Lathe Parts
Utilizing machining lathe parts factories presents numerous advantages that make them indispensable in modern manufacturing:
- Precision: CNC lathes can achieve tolerances of a few microns, making them ideal for critical components.
- Efficiency: High-speed machining reduces production time, which is crucial for meeting market demands.
- Versatility: Capable of machining a wide range of materials, including metals, plastics, and composites.
- Scalability: Production can be easily scaled to meet varying orders without sacrificing quality.
- Cost-Effectiveness: Though initial setup might be costly, long-term savings are realized through reduced material waste and labor costs.
Technological Innovations in Machining Lathe Parts Factories
The industry has not remained stagnant; several technological advancements have emerged, reshaping machining lathe parts factories. Some key innovations include:
CNC Technology
Computer Numerical Control (CNC) machines have revolutionized the manufacturing process. These machines automate the machining process based on programmed instructions, allowing for precise replicability and a dramatic reduction in human error.
Additive Manufacturing
Additive manufacturing, or 3D printing, is finding its place in traditional machining environments. Using techniques that complement CNC machining, factories can produce complex geometries that were once impossible with standard machining alone.
Smart Manufacturing
The concept of smart manufacturing integrates IoT (Internet of Things) devices within machining lathe parts factories. This connectivity enables real-time monitoring and data collection, enhancing efficiency and predictive maintenance capabilities.
Environmental Impact and Sustainability
As the world increasingly prioritizes environmental sustainability, machining lathe parts factories are also adapting. Factors such as waste reduction, energy efficiency, and the recycling of materials are becoming central to manufacturing practices.
Waste Reduction
Implementing lean manufacturing techniques helps minimize waste. By streamlining processes and optimizing material usage, factories can significantly reduce scrap rates.
Energy Efficiency
Modern machines are designed to be more energy-efficient, consuming less power while maintaining high performance levels.
Material Recycling
Recycling metal scrap not only conserves resources but also offers financial benefits, making it a win-win for machining lathe parts factories.
The Future of Machining Lathe Parts Factories
Looking ahead, the outlook for machining lathe parts factories is promising. As industries continue to evolve, these factories are expected to incorporate even more advanced technologies, including:
- Artificial Intelligence (AI): AI can optimize machining processes, predict maintenance needs, and enhance quality control.
- Automation: The rise of robotics will continue to streamline operations, reducing human intervention and increasing safety.
- Enhanced Customization: Growing demand for personalized products will encourage factories to adopt flexible manufacturing systems.
- Global Supply Chain Integration: Improved logistics and global connectivity will allow for more efficient supply chain management.
Conclusion
In conclusion, machining lathe parts factories represent an essential aspect of modern manufacturing dynamism. They are central to delivering high-quality, precision-engineered components that meet the demanding standards of today's industries. As technology advances, these factories are set to evolve further, embracing innovation while prioritizing sustainability. Businesses seeking reliable partners in the realm of metal fabrication can trust in the capabilities and future readiness of machining lathe parts factories. By leveraging cutting-edge technology and adhering to best practices, these entities will continue to excel in delivering the highest quality parts to various sectors.
Why Choose Deep Mould for Your Machining Needs?
At Deep Mould, we pride ourselves on being at the forefront of metal fabrication. Our expertise in machining lathe parts ensures that we deliver products that not only meet but exceed our clients’ requirements. With state-of-the-art technology, a commitment to quality, and a focus on customer satisfaction, we are your ideal partner in navigating the intricate landscape of machining.